2. August 2024 By Oliver Köhn
Display of the machine status in AWS
Due to this quantity, manual monitoring is simply impossible in this case and monitoring must be automated. While problems in cars are often indicated by a loud noise or other easily perceptible signs, matters are unfortunately more complicated in industry. Large volumes of data have to be analyzed automatically using complex processes. However, the benefits of predictive analytics far outweigh the costs. For example, the time required for maintenance is drastically reduced, spare parts are always available, and the uptime of machines and devices is guaranteed. You will find a more detailed description of these points in the next section. We would be happy to advise you on how you too can optimize your processes through predictive analytics in order to minimize costs. The following section describes how your business can benefit from predictive analytics and how such a solution can be implemented in the AWS cloud.
The challenge
Without automated monitoring and analysis of the condition of machines various challenges arise. Three such cases, which occur most frequently without predictive analytics, are summarized in the figure below.
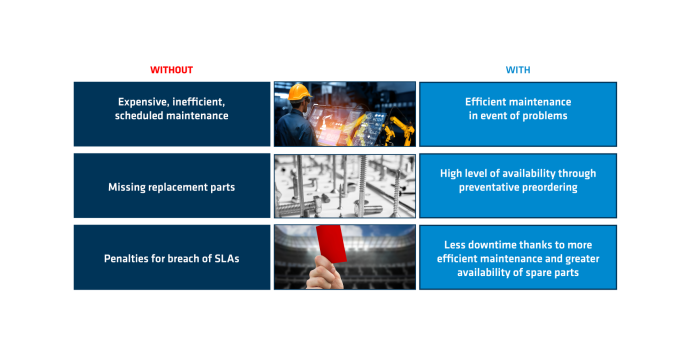
The three greatest challenges that crop up without predictive analytics relate to maintenance, spare parts and service level agreements (SLAs).
- Maintenance: Without predictive analytics, maintenance is significantly less efficient. Devices are usually serviced at fixed intervals. For the majority of these inspections, no problem can be detected on the device, which means that the time invested and therefore the costs would not have been necessary. Using predictive analytics, maintenance depends on the condition of the machine. There is still scheduled maintenance, but at a much lower frequency. Targeted maintenance is carried out in the event of acute problems. Targeted maintenance not only means that maintenance is only carried out when problems are expected, but also that the type of maintenance (specialist technician, workshop, etc.) is selected in line with the specific problem.
- Spare parts: Without predictive analytics, there will also be a lack of required spare parts. If the required part is unavailable, there may be long waiting times when an order is placed. Furthermore, suppliers may charge extremely high fees for speedier delivery times. With an up-to-date overview of the condition of the machines through predictive maintenance, short to long-term spare parts requirements can be identified and corresponding orders can be placed. Typically, acute requirements are visualized in a dashboard for the supply chain team, while automated orders can also be triggered for specific cases.
- Service Level Agreements (SLAs): Without predictive analytics, high financial penalties can result from breaches of SLAs. If a company sells or rents out its devices, SLAs are typically involved. These essentially specify the uptime of devices. Breaches of contract due to excessively long downtimes lead to high fines. Predictive maintenance can significantly reduce these downtimes by means of the two points above - efficient maintenance and the availability of spare parts. The penalties resulting from SLA violations are thus significantly reduced or even completely eliminated.
The points above show how your company can benefit from predictive maintenance. In the following section, we describe how to successfully implement a predictive analytics solution in your company.
The procedure
The implementation of a predictive analytics solution depends on the customer's business model. Every implementation is different and depends on the customer's specific requirements and wishes. The procedure for implementing a predictive analytics solution is an iterative process in which the customer is constantly involved to ensure that the requirements and wishes are implemented effectively. Despite the individual process, this procedure can be formalized to a certain extent. In order to be able to offer a customized solution, various steps are worked through. The diagram below provides an overview of these steps.
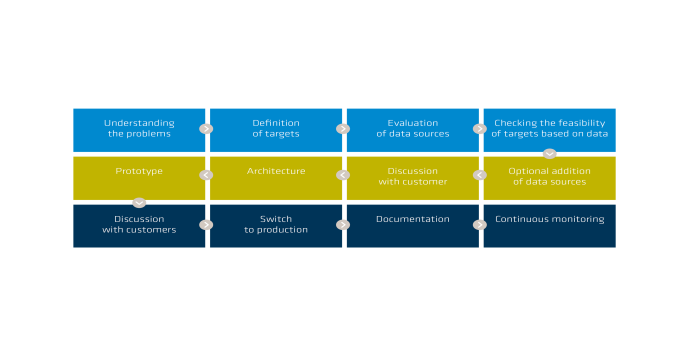
The first step is to understand the specific challenges facing the business. Only once these concerns have been understood can specific goals be defined to solve them. The next step is to evaluate the available data sources. Only with the appropriate data is it possible to achieve the goals. If it is determined that the existing objectives cannot be achieved with the available data, new data sources must be added. This means, for instance, equipping the devices with new sensors. Once sufficient data is available, the information obtained is discussed with the customer. In particular, the extent to which the defined goals can be achieved is discussed. Up to now, the evaluation has been based on historical data in order to define whether this is sufficient to meet the objectives. Once it has been ensured that this is the case, an IT architecture for the predictive maintenance solution with live data is created and a prototype is implemented. The key functions of the predictive analytics solution are implemented in this prototype. After completion, the customer sees a finished solution with the key KPIs, automated messages, etc. This prototype is refined in an iterative process until all customer requirements have been met and the application can go live. In addition to the product, the documentation, which provides a technical and functional description of the application, is also handed over with the go-live. Monitoring is also provided to allow technical monitoring of the application.
The following section describes the technical implementation of such a solution in the AWS cloud.
Implementation with our reference architecture (in AWS)
In this section, we describe the specific implementation of a predictive analytics solution in the AWS cloud. The figure below provides an overview of the architecture.
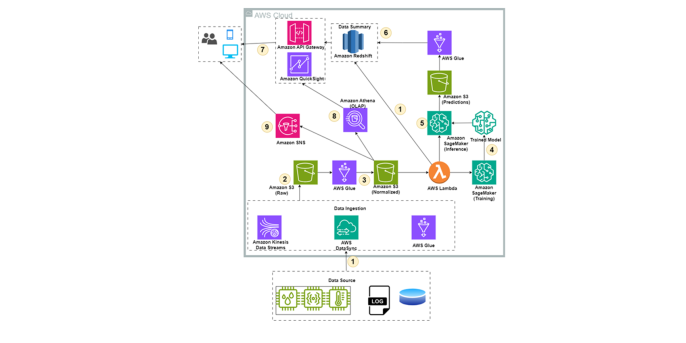
This illustration shows an architecture in the AWS cloud for implementing a predictive analytics solution. The key steps are described below in the form of bullet points in relation to the illustration.
- The first step is to connect the data sources to the AWS cloud. In this example, there are three types of data:
- Streaming: The sensor data (humidity, vibration, temperature, etc.) of the devices provide continuous information and are connected via Amazon Kinesis Data Streams.
- Logs: Log files about the status of devices are connected via AWS DataSync.
- Databases: Information from external databases - e.g. information about the machines - can be connected using AWS Glue.
- The data from the connected sources is stored in an Amazon S3 bucket. It is important that the data is stored in its raw format in an initial step so that the data is not manipulated.
- The data is transported to another S3 bucket using AWS Glue. The raw data is normalized here: Filtering of obvious errors, adaptation of data types, implementation of technical specifications, etc.
- The existing logs show when and which machines had problems. This information - in combination with sensor data - is used to train models which:
- can predict whether a device will have acute problems or not.
- predict the expected remaining useful life of the device (Remaining Useful Life RLU) is.
- Once these models have been trained, they can be applied to the current data and provide live information on the status of the devices. The collected information is stored in another S3 bucket.
- The information is collected in an Amazon Redshift database, which is designed for efficient analytical queries thanks to its OLAP focus.
- Users can use an API gateway to access the existing data via dashboards (QuickSight) or gain access to the Redshift database.
- To gain access to all available data, efficient queries can be performed on the normalized S3 bucket using Amazon Athena.
- If there are obvious problems (which can be defined by fixed rules, for example), automated messages are sent to users (via Whatsapp, Teams, etc.) using Amazon's Smart Notification System (SNS).
The architecture shown in the figure above therefore provides information about the live status of all connected devices (predictive analytics). The information collected can be used in the following ways, among others:
- Data scientists gain valuable insights into the performance of machines
- Technicians are automatically informed about problems
- Supply chain teams can see which spare parts are needed via dashboards
- Predictions are made about which devices are affected by acute problems
The monthly costs for such an architecture vary depending on the use case but can be predicted quite accurately in consultation.
Summary
We have seen that predictive maintenance can optimize processes and significantly reduce costs.
- Essentially, technicians only need to be deployed as necessary
- Spare parts are always available
- Due to a low downtime, no penalties must be paid for the violation of SLAs.
The implementation of a predictive maintenance solution consists of several steps, the main one being to ensure that the defined objectives can be achieved with the existing data. It may be necessary to expand the data sources, e.g. by equipping the devices with new sensors. Finally, we have presented a possible solution in the AWS cloud. Of course, such a solution can also be implemented in another cloud or on-premises.
Please feel free to contact us if you have any questions.